Engineering
Nailii always take customer demand as the center, provide high quality production equipment at the same time also has experienced construction team, after the completion of product development, for customers to develop special installation service program, provide professional facilities and equipment installation construction services, equipment installation for precise positioning, safe construction, project management, assembly and manufacturing, commissioning and testing, acceptance testing, site installation, site acceptance testing, post maintenance during the project construction, in order to ensure the normal and stable operation of the later equipment, to meet the hardware needs of customer production research.
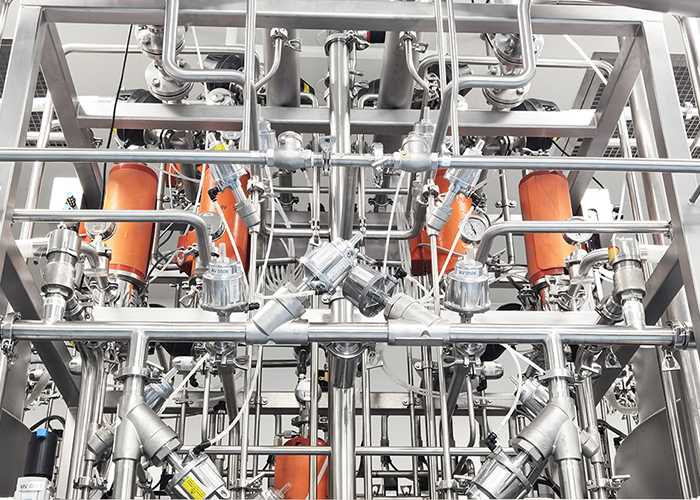
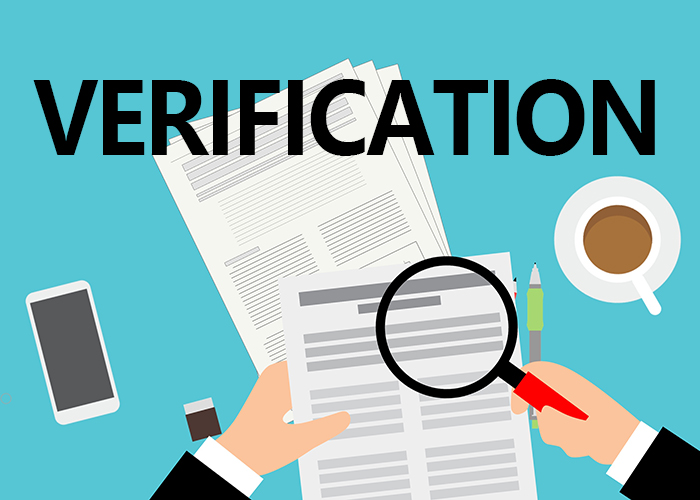
Verification
We can provide you with validation compliance solutions covering the entire product lifecycle, meeting your needs for commissioning, validation, verification and re-validation/re-validation services at different stages. We help your project comply with FDA, EMA, MHRA, PIC/S, NMPA , PMDA certification and WHO pre-validation requirements, and provide complete commissioning and validation services for your project completion.
Our strengths.
* Confidence in your quality audit performance
* Full compliance with regulatory requirements (GMP)
* Dedicated focus on quality-related key attributes
* Reliable and comprehensive documentation and certificates that can be easily integrated into your quality management system
* Expertise direct from the equipment manufacturer and professional level training
Automation control
According to the production process and the control needs of the workshop process, Nailii provides customers with automation software debugging and function upgrade services.
On the one hand, Nailii provides customers with good whole-line control and integration, eliminates automation silos to achieve interconnection between equipment, establishes fully integrated centralized management and control, collects, monitors and archives real-time data for better effective debugging of equipment; on the other hand, Nailii provides single automation equipment, through the PCS process control system to reasonably control the liquid dispensing system, bioreactor CIP station, ultrafiltration system, etc., in line with the ISAS88 standard, simple operation, flexible production functions, thus guaranteeing the reliability of self-control and production, greatly improving production confidentiality and production efficiency.
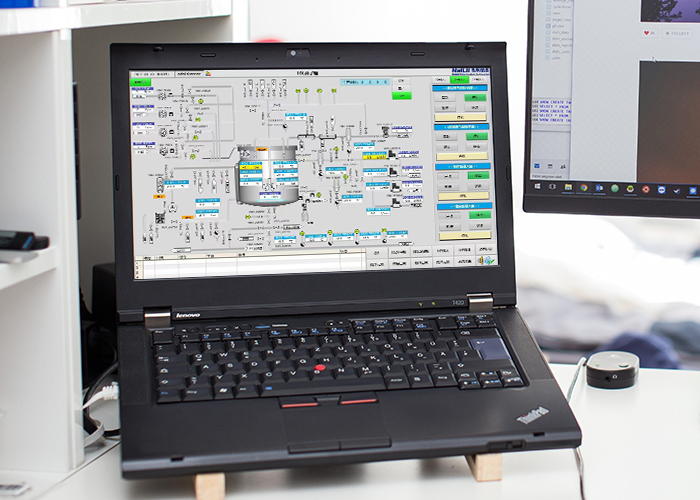
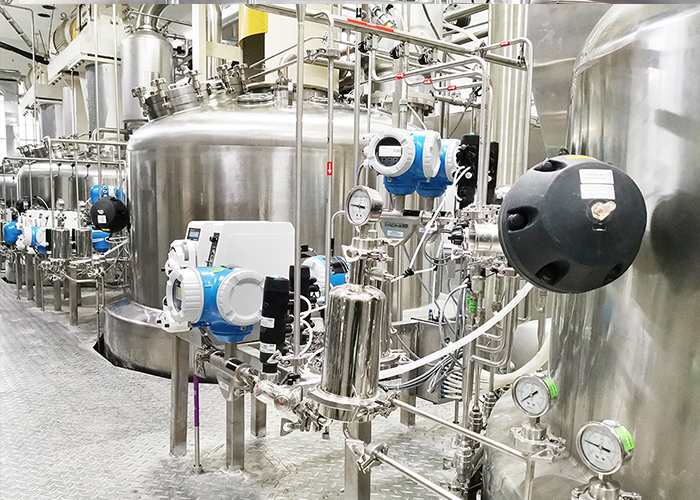
Process optimization
As a value-added partner for drug development in the biopharmaceutical field, we provide a full range of services and application support that can optimize your process, minimize risk and solve problems, from conceptual design, contract testing and research, program development, detailed engineering design to regular preventive maintenance and after-sales service and optimization, our team with professional From conceptual design, contract testing and research, solution development, detailed engineering design to regular preventive maintenance and after-sales service and optimization, our team, with professional competence and reliable quality, insists on the close combination of quality materials, advanced design, strict manufacturing standards and quality assurance system, using production technology and product development capabilities to create first-class customized products for you, providing one-stop service and becoming your most dependable partner.
Testing
Nailii uses a risk-based process validation strategy to develop and implement the best testing services for you, applicable to your specific production environment. With your requirements in mind, our team provides you with scientific, sound and practical advice that translates into customized, individual solutions. With testing services that cover all your critical production steps, we ensure your highest process reliability and the fastest time to market.
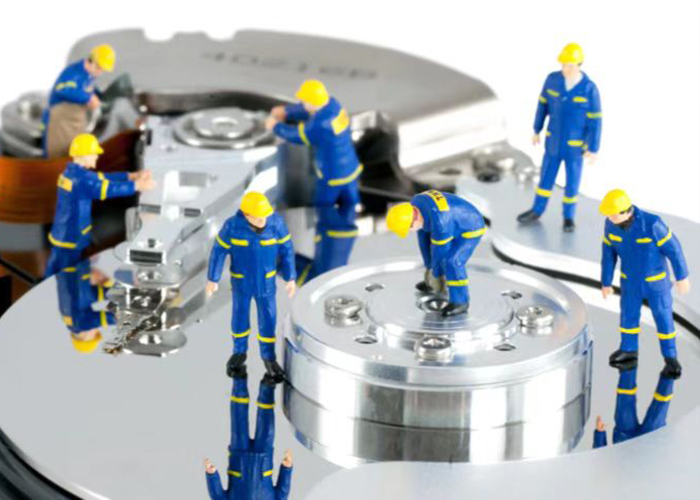
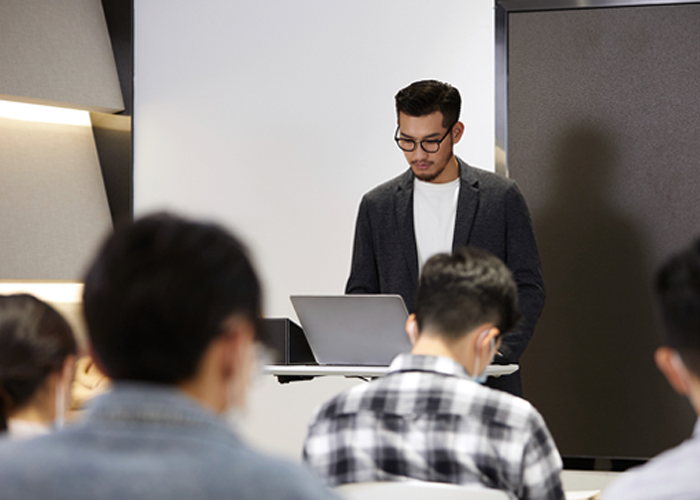
Training
Nailii will also be committed to meet customer skills needs, enhance user experience, the organization sends professional and technical personnel to the customer company staff training and on-site guidance operation, training content includes but not limited to: the basic principles of equipment, equipment operation, routine maintenance, simple troubleshooting, etc.. To ensure that the staff of the target company are proficient in the operation principle and operation method of the instrument, so that they can be better used in daily work production, reduce the cost of manual training and enhance the value of human resources.
Maintenance and spare parts
For equipment failure, damage resulting in normal production and other problems, Nailii will also provide customers with professional maintenance, problem repair and original equipment parts service.The company has a professional after-sales service maintenance team, customer equipment tracking file, open customer equipment life cycle management, and provide preventive maintenance to extend the service life of equipment, while minimizing product loss.
When the equipment fails to operate normally, Nailii will promptly respond to customer needs and provide customers with professional, fast and targeted maintenance services. In addition, Nailii will also be committed to improving the overall user equipment experience, through the most convenient way to provide customers with the configuration of the corresponding original equipment parts.
* High standard after-sales service elite team
* 7x24 hours service window
* Periodic maintenance and return visits
* Professional engineers for parts replacement and maintenance work
* Timely and rapid provision of services or spare parts required by customers
* For spare parts purchase, please contact our sales engineers
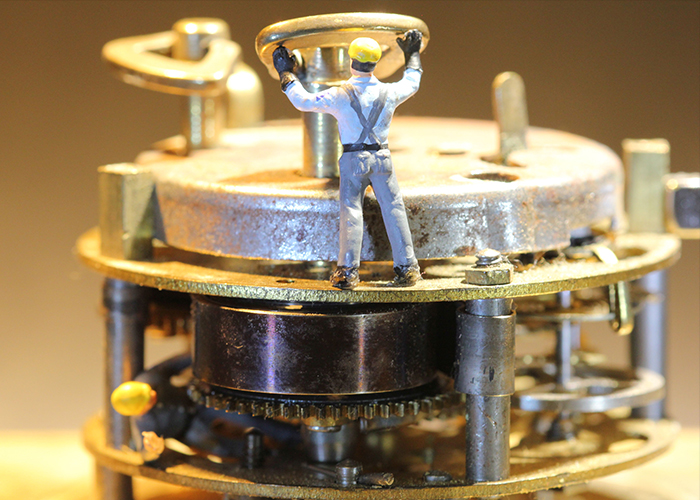